Vetro Cavo
Produzione
I contenitori in vetro cavo prodotti industrialmente si ottengono da un procedimento di soffiatura del materiale fuso in stampi. Le fasi di produzione si possono così sintetizzare:
Fusione:
Le materie prime, contenute in silos, vengono opportunamente dosate, miscelate e immesse nel forno fusorio per mezzo di nastri trasportatori.
Formatura:
Il liquido fuso in uscita dal forno, entra in canali di condizionamento termico e, raggiunta l’opportuna viscosità, viene “tagliato” in gocce di dimensione e peso proporzionale all’oggetto che si vuole realizzare e alla funzione d’uso. La goccia di vetro incandescente (1.200°C circa) giunge, per caduta verticale guidata, allo stampo della macchina formatrice. Il processo tradizionale di “formatura” di un contenitore con il procedimento “soffio-soffio” ha trovato le sue evoluzioni nel processo “presso-soffio” dapprima applicato a contenitori con imboccatura di grande dimensione e recentemente anche nei più difficili contenitori con imboccatura stretta. Queste nuove tecnologie consentono di ottenere contenitori più leggeri con migliori prestazioni meccaniche.
Ricottura:
Alla formatura segue la fase di “ricottura”, procedimento che consente di eliminare le tensioni del vetro mediate riscaldamento preliminare e successivo raffreddamento graduale dell’oggetto fino a raggiungere la temperatura ambiente. Dopo l’avvenuta formatura il contenitore è infatti sottoposto a fortissime tensioni poiché la superficie esterna, a contatto della temperatura ambiente, tende a raffreddarsi più velocemente della superficie interna. Le tensioni generate da questo squilibrio termico potrebbero compromettere la resistenza meccanica del contenitore.
Controllo qualità:
Ogni singolo pezzo prodotto viene sottoposto a verifiche su tutte le caratteristiche: dimensioni, forma, spessore, calibratura delle bocche, integrità, resistenza. I contenitori non considerati idonei vengono espulsi automaticamente dalla linea di imballaggio ed immediatamente riciclati nel medesimo processo produttivo per essere rifusi. L’impiego delle più recenti tecnologie consente la gestione e il monitoraggio di tutto il ciclo produttivo per mezzo di apparecchiature computerizzate, mentre strumenti altamente sofisticati e specializzati assicurano il controllo su base statistica, al fine di ottenere il livello qualitativo del prodotto finito rispondente alle esigenze, funzionali ed estetiche, degli imbottigliatori, della distribuzione fino al consumatore.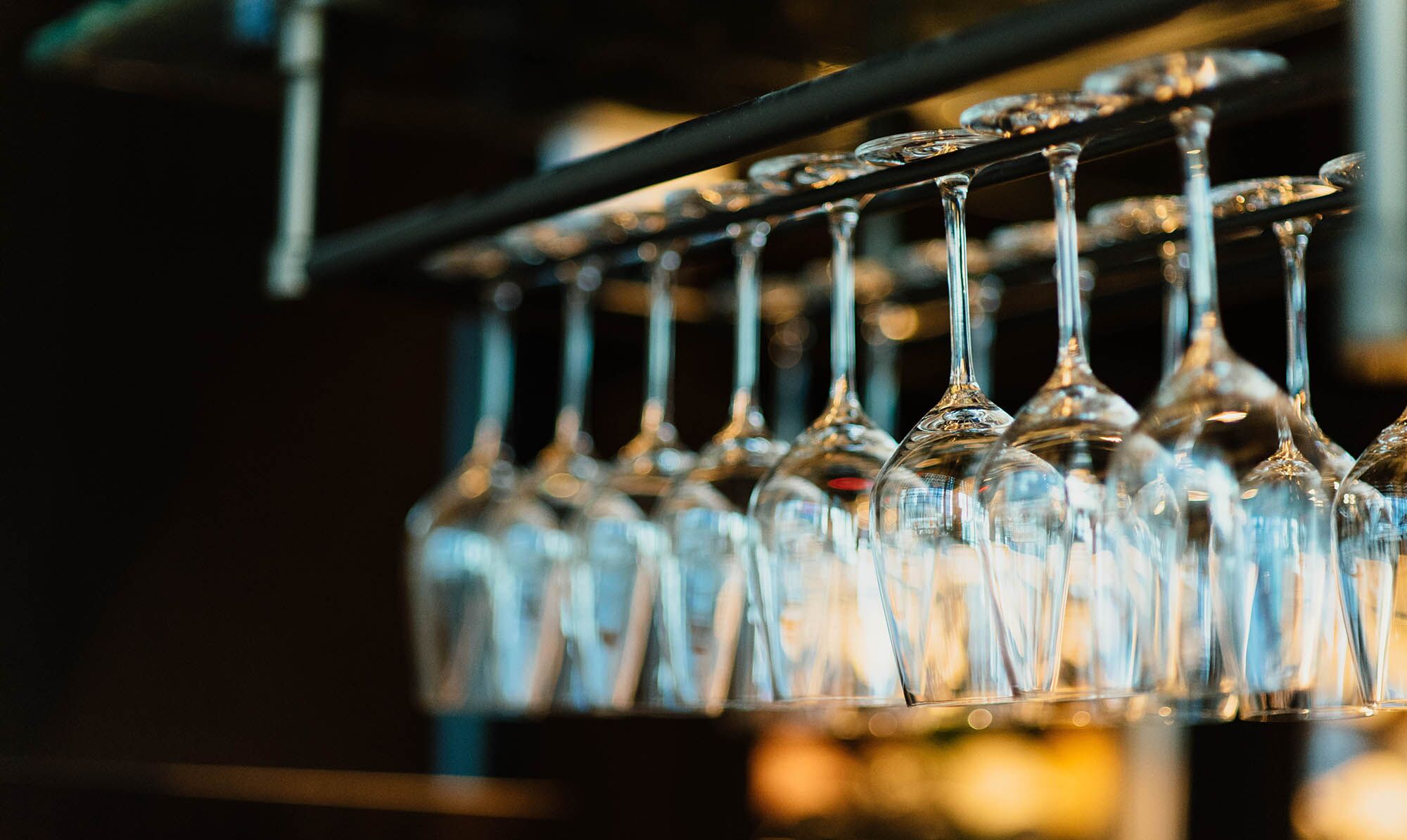